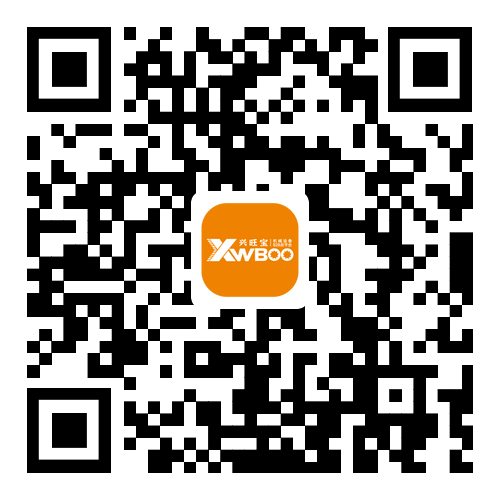
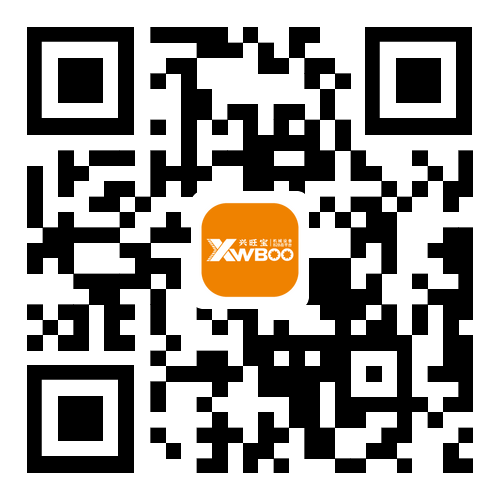
2022-04-16 21:30:04来源:深圳名阀进出口贸易有限公司 阅读量:280
导读:
完整的进口全焊接球阀的焊接工艺介绍
进口全焊接球阀阀体是由碳钢无缝钢管压制成型整体式焊接球阀。由于阀座是由碳化特氟隆密封环及碟形弹簧构成的,所以对压力和温度的变化适应能力强,在标注压力和温度范围内不会产生任何泄滑。
长输管线是性的,是一条能源供给线,从北极圈到赤道,从高山到海底,从高原到沙漠,其间穿过地震带、沼泽地、冻土层、江河、湖泊、山坡。有架设的,有直埋地下,在野外操作,维修困难,要求30年使用寿命。一般输送原油、天然气,虽经处理但含硫,含铁锈及金属颗粒,且要求零级密封,实际的使用环境恶劣和能源供给线的重要性,对管线球阀提出了严格的技术要求.因此,这种高要求的长输管线阀门,一般采用进口品牌的阀门,比较代表性和使用广泛的美国威盾VTON的进口全焊接球阀。
而进口全焊接球阀的焊接方案是非常重要的,所以,本文结合美国威盾VTON的技术人员分析, 对全焊接球阀阀体及焊接材料、焊接方法、焊接结构、焊接工艺及相关试验等方面进行总结,为全焊接球阀的用户使用提供参考。
进口全焊接球阀参数: |
公称通径:DN10-DN600
公称压力:1.6Mpa-4.0Mpa
适用温度:-40℃~200℃
适用介质:水、油、燃气
阀体材质:铸钢、碳钢
连接方式:全焊接
传动方式:手动,蜗轮
1. 阀体材料成分分析
全焊接球阀阀体材料通常采用碳素钢或低合金钢,如 ASTM A105、A694、A350、A516 等,其化学成分对焊接时结晶裂纹的形成有着重要影响。焊接时,焊缝中的 S、P 等杂质在结晶过程中形成低熔点共晶。其中硫对形成结晶裂纹影响大,但其影响又与钢中其他元素含有关,如 Mn 与 S 结合成 MnS 而除硫,从而对 S 的有害作用起抑制作用。Mn 还能改善硫化物的性能、形态及其分布等。因此,为了防止产生结晶裂纹,对焊缝金属中的 Mn/S 值有一定要求。Mn/sS 值多大才有利干防止结晶裂纹,还与含碳量有关。含 C 量愈高,要求 Mn/S 值也愈高。Si、Ni 及杂质的过多存在也会增加 S 的有害作用。
严格控制阀体材料采购时的化学成分,制定相关的材料采购标准,是有效避免进口全焊接球阀焊接时产生结晶裂纹的有效途径之一。
2. 焊丝与焊剂选择
(1)焊丝材料选择 焊丝主要作为填充金属,向焊缝添加合金元素,直接参与焊接过程中的冶金反应,其化学成分和物理性能不仅影响焊接过程中的稳定性、焊接接头性能和质量,同时还影响着焊接生产率。
焊丝材料的选择主要根据阀体材料来进行。对常用阀体材料,通常所选用的焊丝材料有碳素钢焊丝如 H08MnA、低合金钢焊丝如 H10Mn2。同时,焊丝直径的选择对焊缝形状也有着较大影响,在焊接电流、电弧电压、焊接速度一定时,焊缝熔深与焊丝直径成反比,熔宽与焊丝直径成正比。对于全焊接球阀常采用的埋弧自动焊,其焊丝直径一般为 2.5~6mm。
(2)焊剂材料选 择焊剂在焊接过程中起隔离空气、保护焊缝金属不受空气浸害和参与熔池金属冶金反应的作用。当焊丝确定后,配套用的焊剂则成为关键材料,它直接影响焊缝金属的力学性能(特别是塑性及低温韧性)、抗裂性能、焊接缺陷发生率及焊接生产率等。
这就要求焊剂必须具有良好的冶金性能和工艺性能;颗粒度符合要求(普通焊剂颗粒度为 0.45~2.50mm,0.45mm 以下的细粒不得大于 5%,2.50mm 以上的粗粒不得大于 2%;细颗粒度焊剂粒度为 0.28~1.425mm,0.28mm 以下的细粒不得大于 5%,1.425mm 以上的粗粒不得大于 2%);含水量 w(H2O)≤0.10%;机械夹杂物的含量不得大于 0.30%(质量分数);含硫磷量 w(S)≤0.060%,w(P)≤0.080%。
根据所选用焊丝材料,及阀体材料化学成分,焊剂多选用高硅型熔炼焊剂或高碱度烧结型焊剂。
热力热水用的进口全焊接球阀结构: |
①一体式全焊接球阀,不会有外部泄漏等现象;
②采用浮球结构,斜面弹性垫圈保证密封圈紧压在球体之上,即使在压力不稳定的情况下,阀门可以保证严密;
③由于阀体材料跟管道材质一样,不会出现应力不均,也不会由于地震及车辆经过地面时而产生变形,管道耐老化;
④密封环本体采用含量20%Carbon(碳素)的RPTFE材质,保障*无泄漏;
⑤直埋式全焊接球阀可以直接埋于地下,不用建高大型阀门井,只需在地面上设置小型浅井,大大节省施工费用及工程时间;
⑥可根据管道的施工及设计要求,调整阀体的长短和阀杆的高度;
⑦球体的加工过程有*的计算机检测仪跟踪检测,加工精密度非常精密,操作轻便;
⑧不需要维护,调整及润滑,易于安装,阀体不含沉重且不可靠的铸件。
焊接坡口形式
全焊接球阀采用埋弧自动焊,配合以空冷或风冷方式进行焊接。
长输管线球阀锻钢阀体壁厚通常在 40~50mm 以上,宜采用窄间隙坡口埋弧焊,坡口底层间隙为 8~35mm,坡口角度为 1°~7°,每层焊缝道数为 1~3,常采用工艺垫板打底焊。为使焊丝送达窄坡底层,需设计能插人坡口内的窄焊嘴,焊丝向下伸长度常取 45~75mm,以获得较高熔敷速率。焊接时采用焊剂,其颗粒度一般较细,脱渣性应特好,并满足高强韧性焊缝金属性能。为保证焊丝和电弧在深而窄坡口内的正确位置,必要时须采用自动跟踪控制。
焊接过程及分析
1. 影响焊缝形状、性能的因素
(1)焊接艺参数的影响
1)焊接电流。当其他条件不变时,熔深与焊接电流变化成正比,电流小,熔深浅,余高和宽度不足;电流过大,熔深大,余高过大,易产生高温裂纹。
2)电弧电压。电弧电压与电弧长度成正比,在相同的电弧电压和焊接电流时,如果选用的焊剂不同,电弧空间电场强度不同,则电弧长度不同。当其他条件不变时,电弧电压低,熔深大,焊缝宽度窄,易产生热裂纹;电弧电压高时,焊缝宽度增加,余高不够。埋弧焊的电弧电压是依据焊接电流调整的,即一定焊接电流要保持一定的弧长才可能保证焊接电弧的稳定燃烧,所以电弧电压的变化范围是有限的。
3)焊接速度。焊接速度对熔深和熔宽都有影响,通常情况下熔深和熔宽与焊接速度成反比。焊接速度对焊缝断面形状也有影响,一般焊接速度过小,熔化金属量多,焊缝成形差;焊接速度较大时,熔化金属量不足,容易产生咬边。实际焊接时,为了提高生产率,在提高焊接速度的同时必须加大电弧功率,才能保证焊缝质量。
4)焊丝直径。焊接电流、电弧电压和焊接速度一定时,熔深与焊丝直径成反比关系,但这种反比关系随电流密度的增加而减弱。
(2)工艺条件对焊缝成形的影响
1)焊缝坡口形状、间隙的影响。在其它条件相同时,增加坡口深度和宽度,焊缝熔深增加,熔宽略有减小,余高显著减小。
2)焊剂堆高的影响。焊剂堆高应保证在丝极周围埋住电弧,一般在 25~40mm。当使用黏结焊剂或烧结焊剂时,由干密度小,焊剂堆高比熔炼焊剂高出 20%~50%。焊剂堆高越大,焊缝余高越大,熔深越浅。
3)焊丝、焊嘴与工件倾角对焊缝成形也有较大的影响。在全焊接球阀焊接过程中,应尽量保证焊嘴、焊丝垂直干工件表面。
2. 焊接及分析
焊接试验采用圆筒进行,材料 A105。其主要目的是试验验证和确定阀体原材料、焊丝直径、焊剂牌号,优化焊接坡口结构及焊接参数,预测和控制焊接时温度变化、变形量和焊接残留应力,为全焊接球阀的生产设计提供参考依据。焊接试验系统由电流电压测量系统、位移变形测量系统、温度测量系统三部分组成。
1)焊接时温度侧定。根据温度测定的结果(如图 1 所示),在球阀焊接时,控制层间温度不超过阀座密封圈的安全使用温度 150℃,不会对阀门密封性能造成影响。
距离焊缝中心 25mm 处的温度变化曲线图(图 1)
图 1 距离焊缝中心 25mm 处的温度变化曲线图
2)焊接变形的测定。圆筒焊接采用内径为 600mm,厚度 50mm 左右的圆简进行。焊接时圆筒两端无束缚,焊接完成后,测得的圆筒变形轴向方向约为 2.5mm,径向方向约为 1.5mm。在全焊接球阀设计过程中,需考虑此焊接变形对球阀密封性能的影响,适当调整阀座与阀体之间的配合间隙。
焊接时可采用不同的辅助方式如风冷、振动,改善焊接时工件的变形。通常情况下,振动焊接时变形较小,风冷其次。
3)焊接残留应力的测定。焊后通过不通孔法测量焊接残留应力。焊接残留应力分布曲线如图 2 所示。
残留应力分布图(图 2)
图 2 残留应力分布图
侧定结果表明,距离焊缝中心位置越远,残留应力越小。对球阀阀体焊缝结构进行合理的设计,可有效降低阀体焊接后因变形而产生的残留应力。同时,焊接时采用不同的辅助方式如振动、风冷,可不同程度上降低焊接后残余应力。通常情况下,振动焊接可有效释放焊接后的残留应力。
焊接完成后,X 射线探伤和超声波探伤*合格;力学性能评定,拉伸试验、冲击试验和侧弯试验合格;焊缝热影响区按 JB4708 测定合格。